Statement of Health and Safety Policy
General
G&B Electronic Designs recognises that complying with the Health and Safety at Work etc. Act 1974 (and regulations made under it) is a legal requirement, not a matter of choice.
Our policy is to:
- Prevent accidents and work-related ill health, so far as is reasonably practicable.
- To monitor the mental health of our workforce and to ensure no member of our team leaves work feeling worse than when they arrived.
- Provide adequate resources to control health and safety risks arising from work activities.
- Maintain safe and healthy premises, provide and maintain plant, machinery and equipment, and ensure safe storage, handling and use of substances.
- Ensure systems are in place to properly assess risk, maintain, monitor and, where necessary, improve safety and health performance throughout all areas of our activities.
- Implement emergency procedures in case of fire or other significant incident.
- Ensure there is adequate first aid provision and report incidents required by law.
- Provide sufficient information, instruction and training to ensure employees are competent to carry out their work.
- Ensure there is adequate supervision commensurate with risk and complexity of task.
- Properly communicate and consult on health and safety matters at all levels of the business.
- Work closely with contractors, suppliers and other stakeholders to ensure adequate levels of health and safety performance are achieved and maintained.
Review
This policy, and the way it is operated, will be reviewed annually or more often if the business changes in nature and size or we believe it is no longer valid.
Any revisions made to improve safety performance will be effectively communicated to employees and all other interested parties.
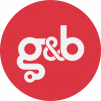
Electronic Manufacturing Services (EMS)
Copyright © 2025 | G&B Electronic Designs Ltd
Site map
|
|
|
 |
Manufacturing Services
|
|
Contact
T: 01420 474188
F: 01420 485277
G&B Electronic Designs Ltd
54 Woolmer Industrial Estate
Bordon
GU35 9QF
|